Custom Rubber Molding
HOME >> CAPABILITIES >> Rubber Manufacturing
Rubber Manufacturing
Precision Rubber Manufacturing: Crafting Performance
At Rich-Rubber, we transform specialized rubber compounds into durable solutions through advanced shaping techniques. Rubber molding is the process where uncured rubber is formed within sealed metal molds under controlled heat and pressure. This initiates curing – a chemical reaction that permanently strengthens the material, resulting in dimensionally stable, resilient components engineered for demanding environments.
Three Core Molding Methods
Selecting the appropriate molding method ensures optimal performance, efficiency, and value for every unique application.
1.Compression Molding
Pre-measured rubber material is placed into a heated mold cavity. Hydraulic pressure then compresses the material, filling the cavity as heat activates the curing reaction. This approach excels for creating larger, thicker, or simpler-geometry parts requiring material strength. Its tooling simplicity makes it practical for limited-run production or custom components across sectors like industrial machinery or heavy equipment.
2.Transfer Molding
Uncured rubber is preheated in a separate chamber (“pot”) above the mold. A plunger forces this softened material through feed channels into the closed, heated mold cavities. Transfer molding bridges the gap between compression and injection techniques, offering finer detail capture and tighter tolerances than compression molding, while requiring less complex tooling than full injection systems. It efficiently handles inserts and moderate production volumes for technical applications.
3.Rubber & Silicone Injection Molding
Continuous material pellets are fed into a heated barrel, liquefied, and forcefully injected into closed molds under high pressure. Both traditional rubber stocks and liquid silicone rubber (LSR) excel with this method. It delivers exceptional dimensional consistency, intricate feature reproduction, and the fastest cycle times, making it ideal for complex or tiny components and high-volume production requirements.
Advanced Material Integration
Many applications require a permanent bond between rubber and other materials like metals or plastics. Rich-Rubber masters techniques to achieve inseparable bonds for enhanced component functionality.
Adhesive Bonding & Vulcanization
We employ specialized chemical adhesives or heat-activated vulcanization bonding to create molecular-level connections between rubber and substrate surfaces. These methods ensure durable adhesion in critical assemblies like rubber-to-metal mounts, bonded seals, or composite structures facing dynamic loads, fluids, or extreme conditions.
1.Overmolding
A rigid base component (e.g., plastic skeleton) is precisely positioned, and rubber is molded directly onto its surface in a secondary operation. This creates unified parts featuring integrated properties – like a non-slip grip fused to a tool handle, or a flexible seal formed onto a rigid plastic housing – combining aesthetics, comfort, and functionality without secondary assembly.
2.Insert Molding
Metal or plastic inserts are placed directly into the rubber mold cavity. Rubber is then injected around them. As the rubber cures, it mechanically locks the insert in place. This process is key for creating electrically conductive pathways in seals, mounting studs in vibration isolators, or structurally reinforced hybrid components, eliminating unreliable gluing operations.
Why Partner with Rich-Rubber?
At Rich-Rubber, manufacturing excellence starts with deep material science and ends with rigorous quality control. We don’t just press rubber – we engineer solutions. We partner with you to select the optimal molding or bonding method based on your performance targets, production needs, and environmental challenges. Our certified processes guarantee traceable, compliant parts that withstand the test of duty.
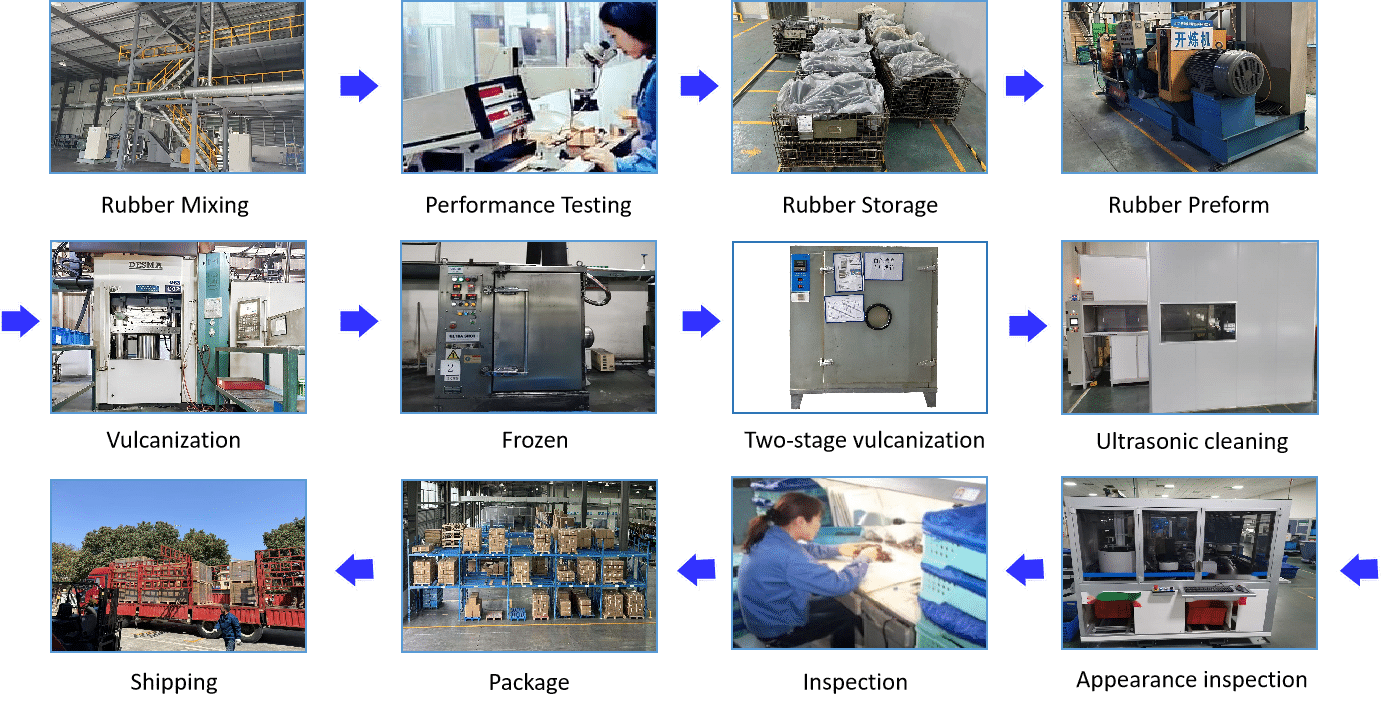
Contact Us today to learn more about our custom rubber manufacturing services and how we can help you with your next project.