Understanding Rubber to Metal Bonding: Core Industrial Advantages
HOME >> News >> Understanding Rubber to Metal Bonding: Core Industrial Advantages
News
Understanding Rubber to Metal Bonding: Core Industrial Advantages
Author: Site Editor Publish Time: 07-15-2025 Origin: Site
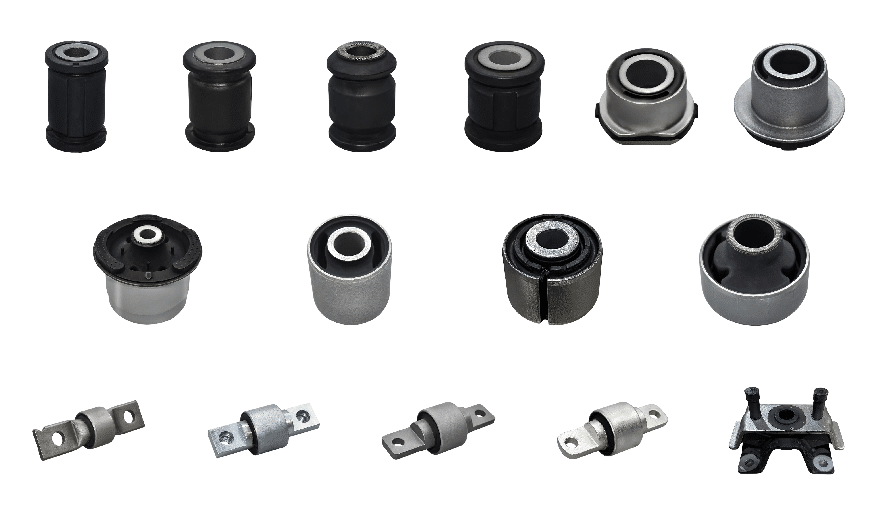
Understanding Rubber to Metal Bonding: Core Industrial Advantages
Rubber demands permanent bonding to substrates to achieve critical functionality across static applications like sealing systems and dynamic environments such as vibration-prone machinery. This integration creates hybrid components where metal provides structural integrity while rubber delivers essential flexibility and damping properties, surpassing mechanically assembled solutions in consistency and performance longevity. The operational success of these bonded systems depends fundamentally on precisely engineered chemical and physical adhesion – requiring quantified bond strength to endure extreme shocks, hydraulic pressures, and high-frequency vibrations without delamination.
Achieving fail-safe bonding requires meticulous control across multiple technical phases. Surface preparation of metal substrates through grit ballasting or chemical etching establishes micro-roughness for mechanical keying, while specialized primers modify surface energy for chemical receptiveness. The selection of cross-linking adhesives must align precisely with both the substrate’s metallurgy and the rubber compound’s chemistry. Similarly decisive is the vulcanization process: temperature gradients, pressure consistency, and curing duration are scientifically calibrated to activate molecular bonding without thermal degradation of elastomer. Current industry leaders extend these techniques beyond metal to bond rubber with Bakelite, phenol resins, engineered thermoplastics, and reinforced textiles – addressing unique application requirements like electrical insulation or chemical resistance.
Validating bond integrity necessitates comprehensive in-house testing protocols, including accelerated aging, salt spray exposure, and dynamic fatigue simulation replicating a decade-long service life. Technically optimized rubber-to-substrate bonding proves indispensable in high-stress sectors: automotive engine mounts surviving torque reversals, aerospace dampeners enduring -55°C to 150°C thermal cycling, or hydraulic seals maintaining integrity at 300 bar pressures. Industry validation manifests through consistent performance in these critical applications, where bonded solutions reliably outperform mechanical alternatives by 300-500% in operational lifespan under equivalent conditions.